Gas purification plays a critical role in different industrial sectors where high purity gas is required. Some applications that require gas purification include semiconductor manufacturing and medical applications.
MOFs are the most recently developed porous materials; they are hybrid materials with superhigh surface areas and tunable surface chemistry that allow increased selectivity. In adsorption separations with MOF materials, gas adsorption processes are improved by framework flexibility and chemical interaction. In some cases, MOFs can perform structural transformations-like gate opening for selective separation.
Some advantages of MOF materials for gas separation are:
Tunable pore size for sieving effect
Functional sites for specific molecular recognition
Dual functionality to optimize separation performance
MOF’s structural and chemical features are critical for gas separations; control over pore dimensions facilitates size or shape-dependent separations (molecular sieving effect), including carbon dioxide capture, alkyne/olefin, olefin/paraffin, alkene, or alkane isomers. The incorporation of specific functional sites allows recognition of gas molecules through chemical binding interactions, including hydrogen bonding, coordination, and even covalent bonds.
Other MOF applications in gas separations include natural gas purification, acetylene/carbon dioxide, xenon/krypton separations, and toxic gas removal.
Case Study
Separating hydrocarbons
Separating ethane and ethylene is still a difficult process in todays chemical industry. Metal-organic frameworks offer a new route to generate high-purity gases.
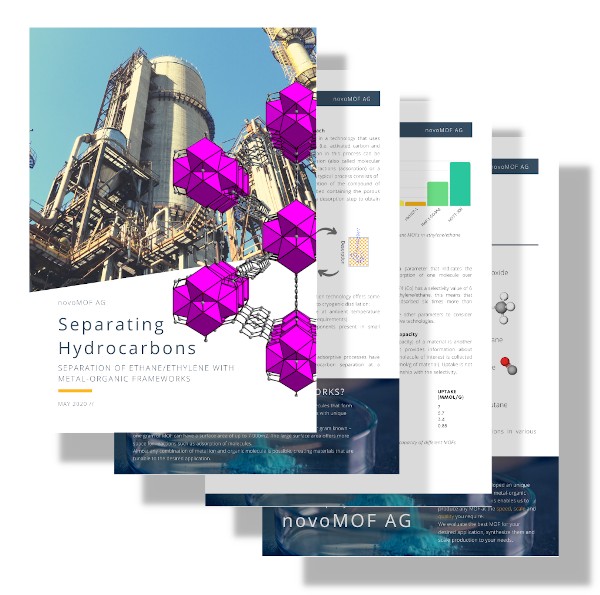
Key points covered:
- Comparison of different separation processes
- MOF specific properties
- Benefits of MOFs for hydrocarbon separation